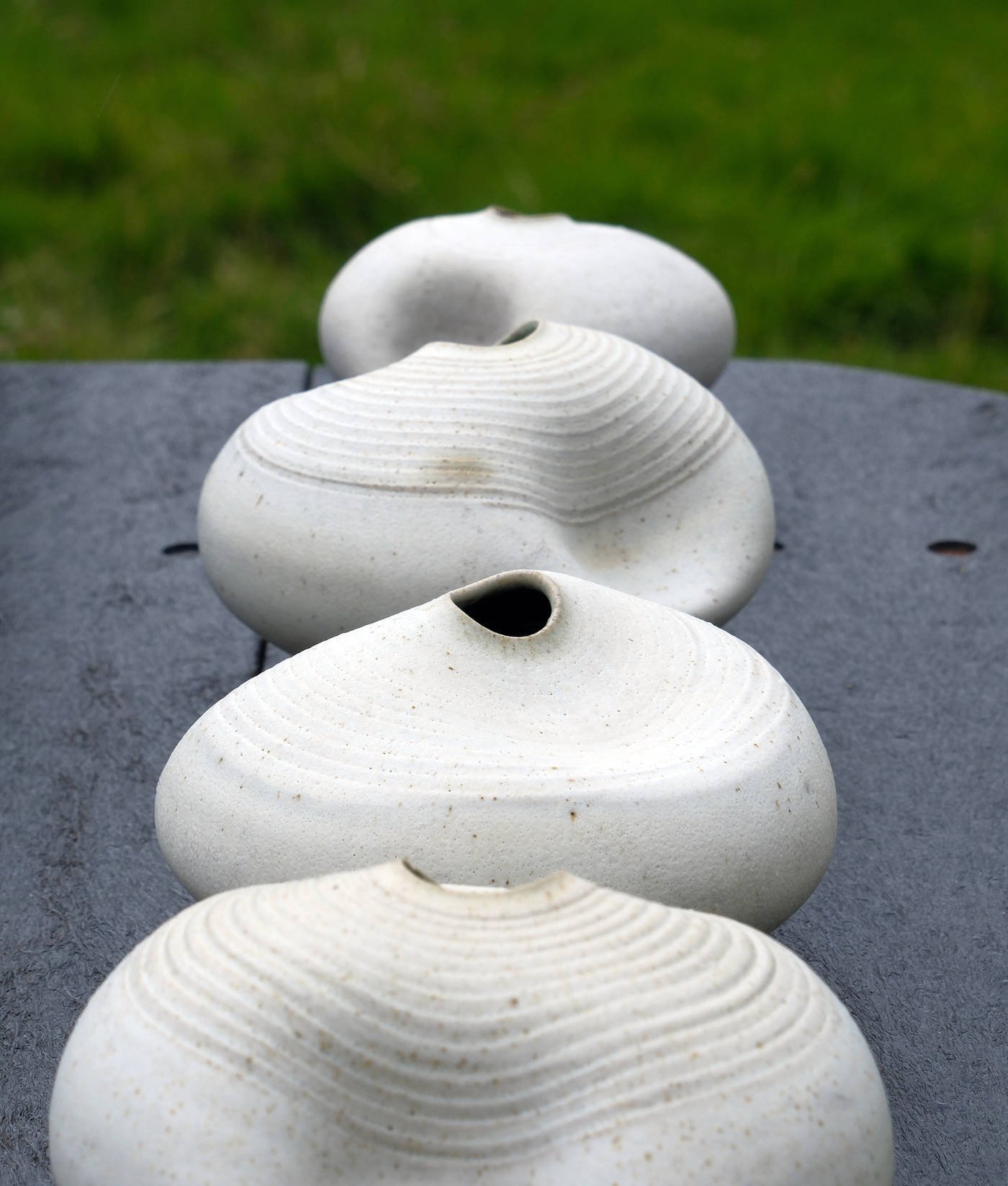
Process
On Dimple Pots
The dimple pots series represents an ongoing exploration of form, texture, and material, evolving through experimentation…
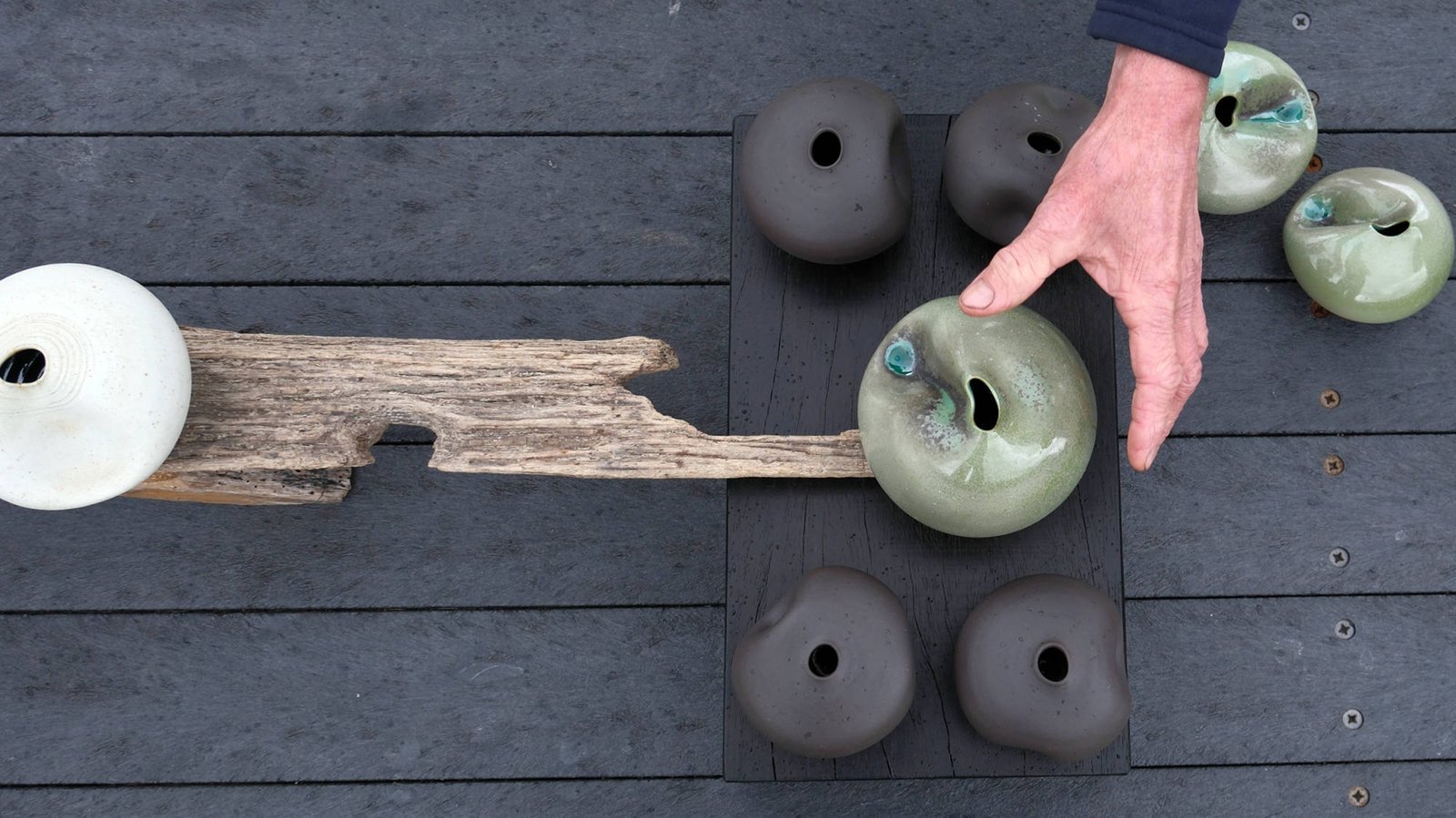
My ceramic practice is one of continual evolution, where each piece serves as a culmination of learned techniques and a springboard for innovations. This is particularly evident in the creation of my dimple pots, a series that represents an ongoing exploration of form, texture, and material. These pots, though distinct in their individuality, form a cohesive family — an ongoing collective that speaks to the nuanced relationships between shape, surface, and technique.
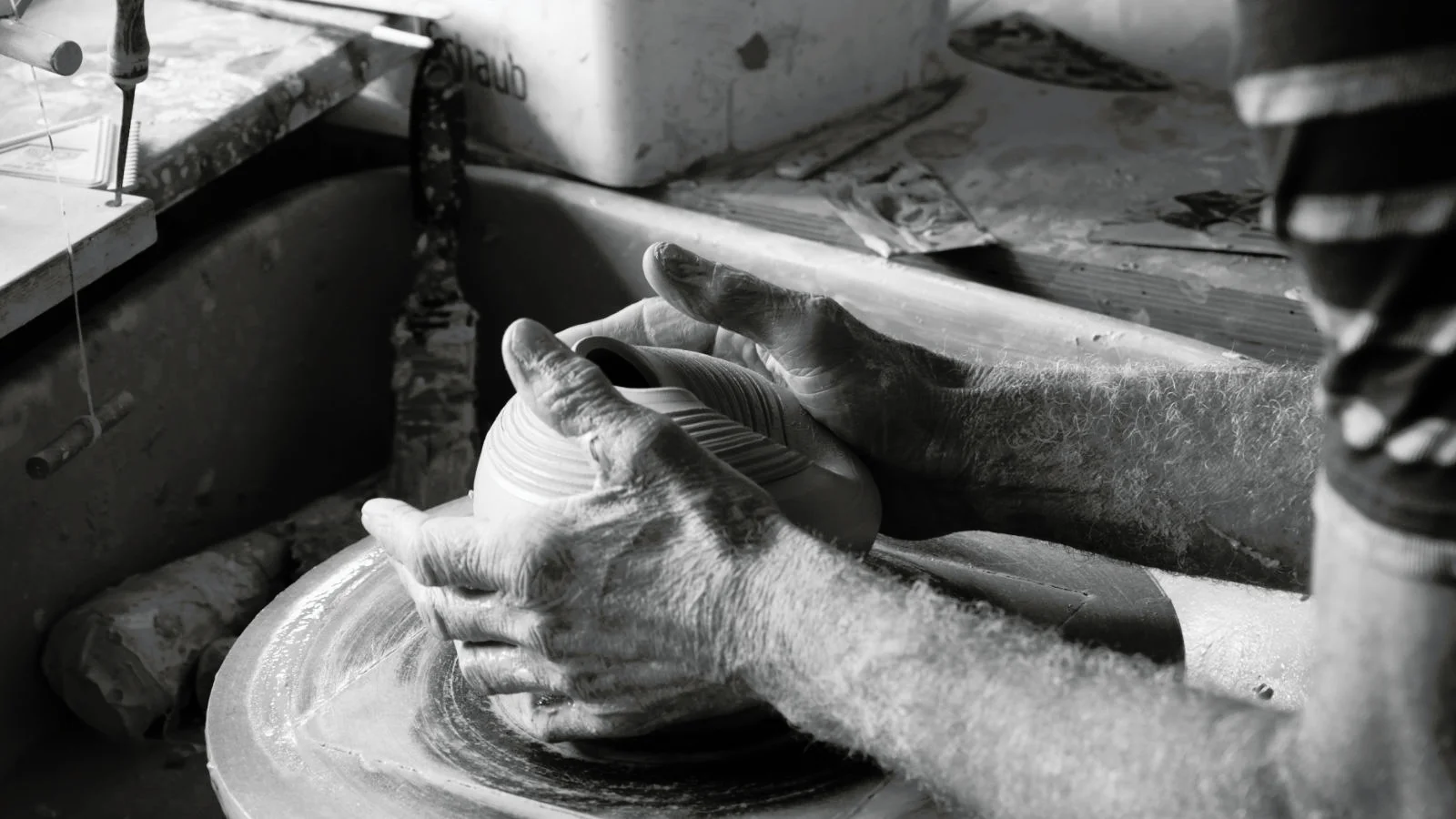
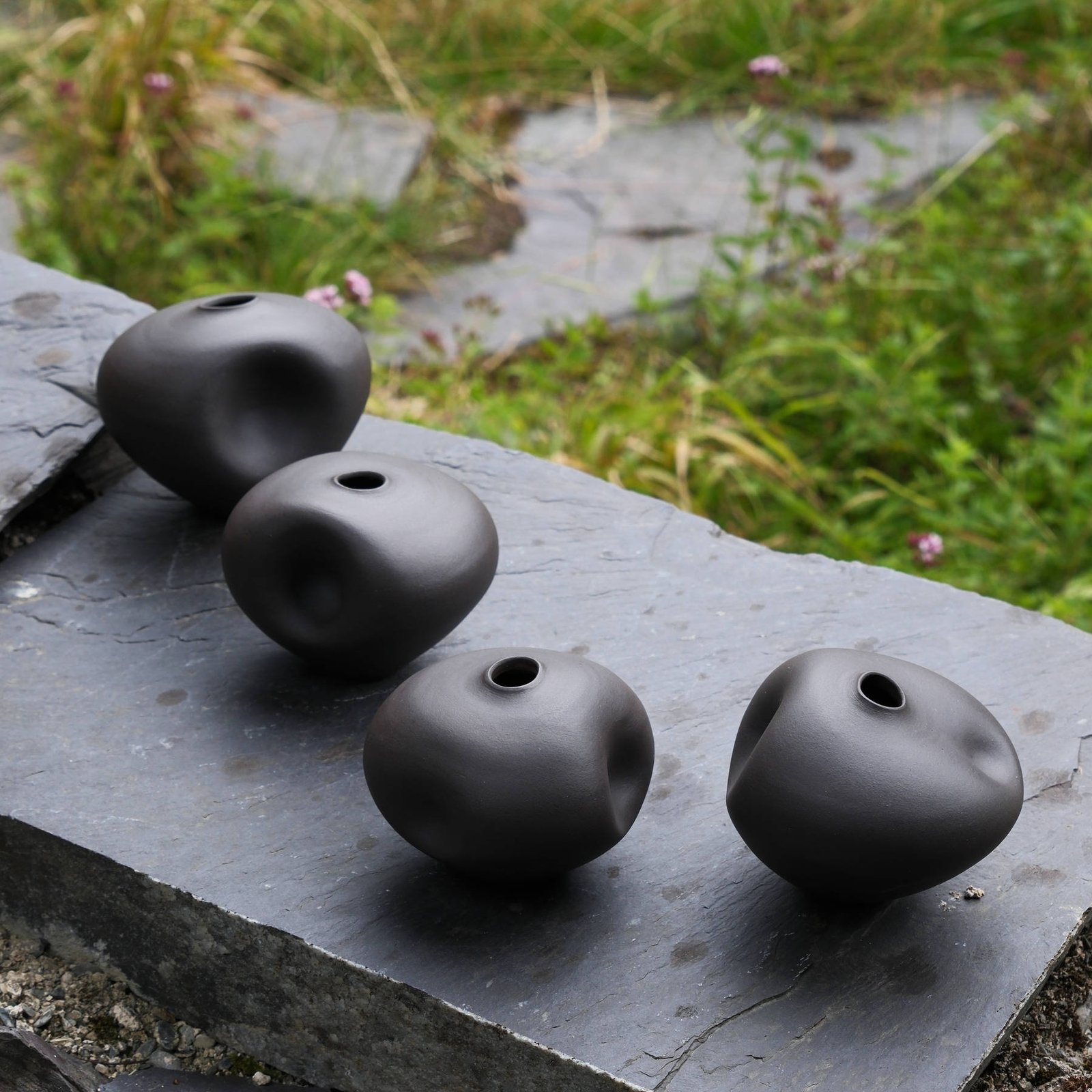
Surface, form(s)
My earlier works in this series reflect a deep fascination with the subtleties of indentation and the visual connection between individual pots. Crafted from black porcelain, these pieces are polished to a smooth finish and fired at a stoneware temperature, resulting in a durable yet refined exterior. What’s intriguing about these dimple pots is their duality — while the inside is glazed, the outside remains unglazed, allowing the raw, tactile quality of the porcelain to come through. This contrast invites interaction, urging the viewer to explore the pots from different angles, where the front and back reveal subtle shifts in the dynamics of their form.
As the series evolved, so did the materials and techniques. I began experimenting with stoneware, incorporating glaze firings that introduced new dimensions to the dimple pots. In these iterations, I added glass powder to the glaze—a delicate inclusion that, when fired, created a striking glassy contrast against the matte finish of the stoneware. This interaction between the glossy and matte surfaces adds a layer of complexity, as the glass slides down the pot, pooling into crevices and creating a dynamic interplay of textures.
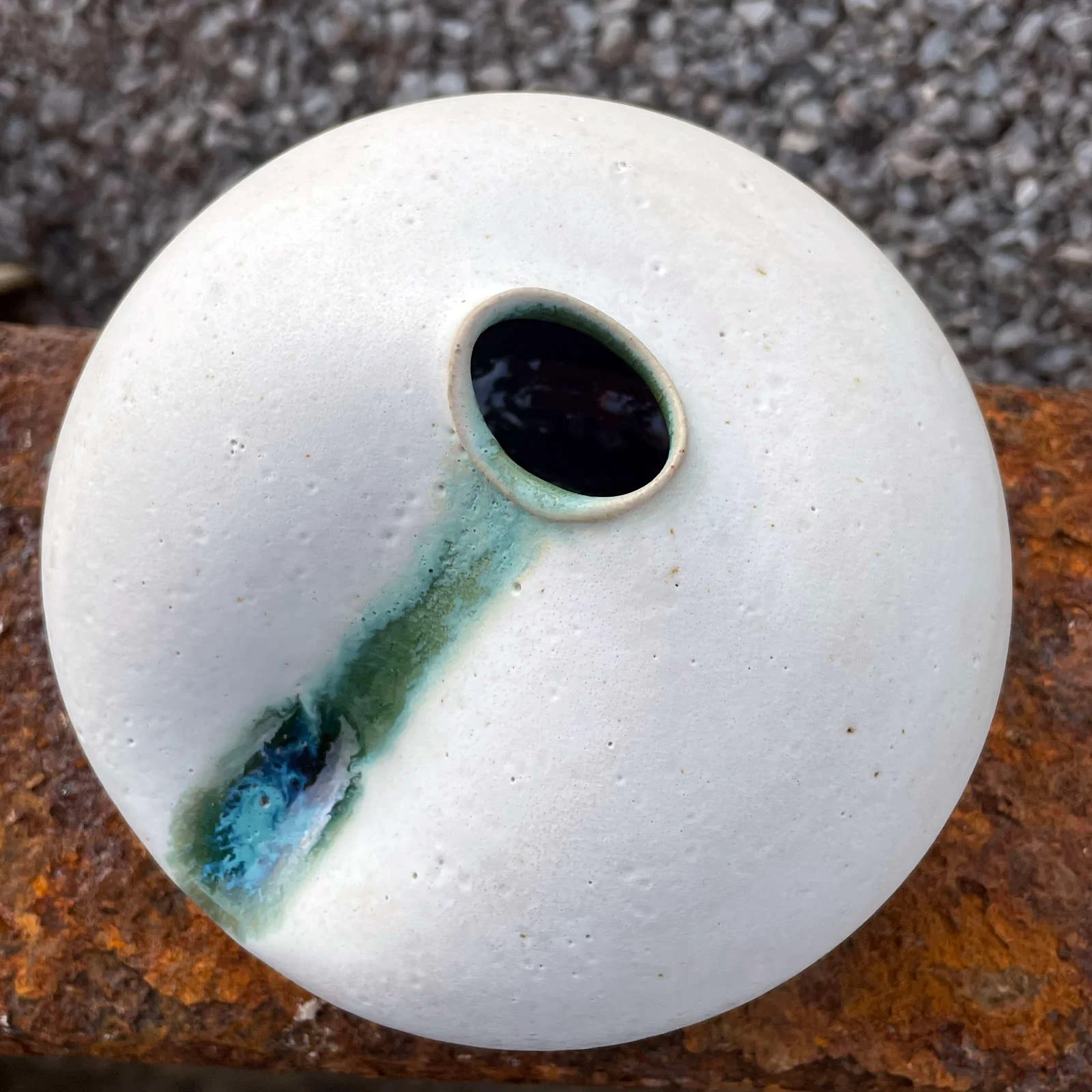
Metals
Copper has also become a central element in the evolution of the dimple pots. Copper is a fascinating material in ceramics, capable of producing a wide range of finishes depending on the firing atmosphere. In a gas-fired reduction kiln, for example, copper can be starved of oxygen, leading to rich, varied hues ranging from deep reds to soft pinks. The application of this copper glaze has been an experimental journey — using a spray gun I discovered that when the gun spatters, it creates droplets that, when fired, surround the copper and result in unique, unpredictable patterns. This serendipity is part of the beauty of ceramics; while some aspects can be controlled and replicated, others are purely one-of-a-kind, the result of momentary interactions between material, technique, and heat.
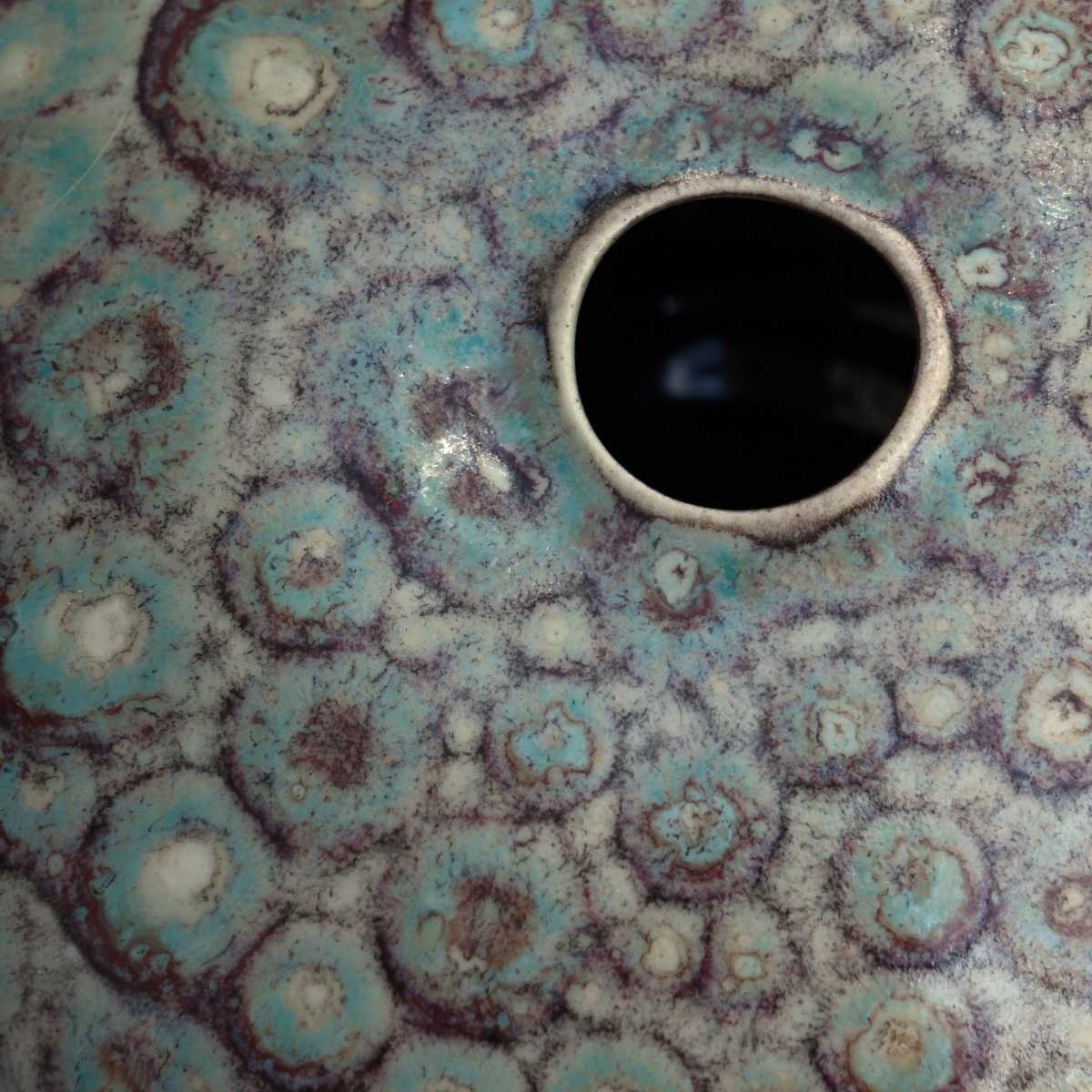
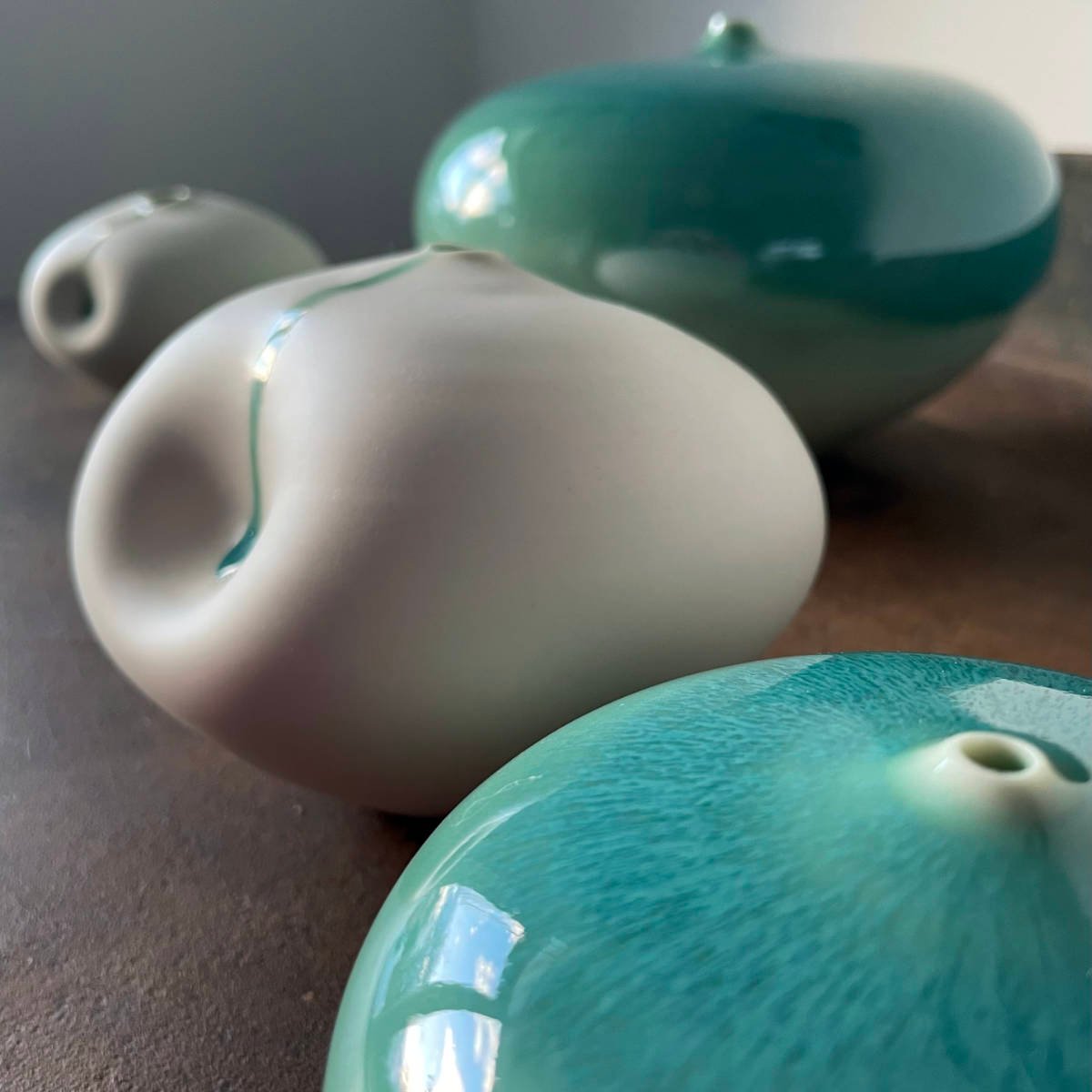
Anatomies
The development of the dimple pots has been an ongoing process. As I continue to explore the form, I’ve been particularly interested in the neck of the pots. Deliberately distorting the pot, the neck changes in response, introducing an element of surprise and tension in the design. Each pot in the series has a foot, a belly, a shoulder, and a neck, and by manipulating these elements, I create lines and ledges that encourage the glaze to pool in certain areas during firing. This technique adds depth and interest to the surface, highlighting the intricate relationship between the form and its finish.
neck
lip
shoulder
belly
Development
In essence, the dimple pots are more than just vessels; they are a testament to the journey of discovery inherent in the ceramicist’s process. Each pot carries a history of experimentation and the thrill of creating something new and unexpected. The evolution of these pots mirrors the evolution of my practice — a continual refinement, a deeper understanding of materials, and an ever-present curiosity about what lies just beyond the horizon in the world of my ceramics.
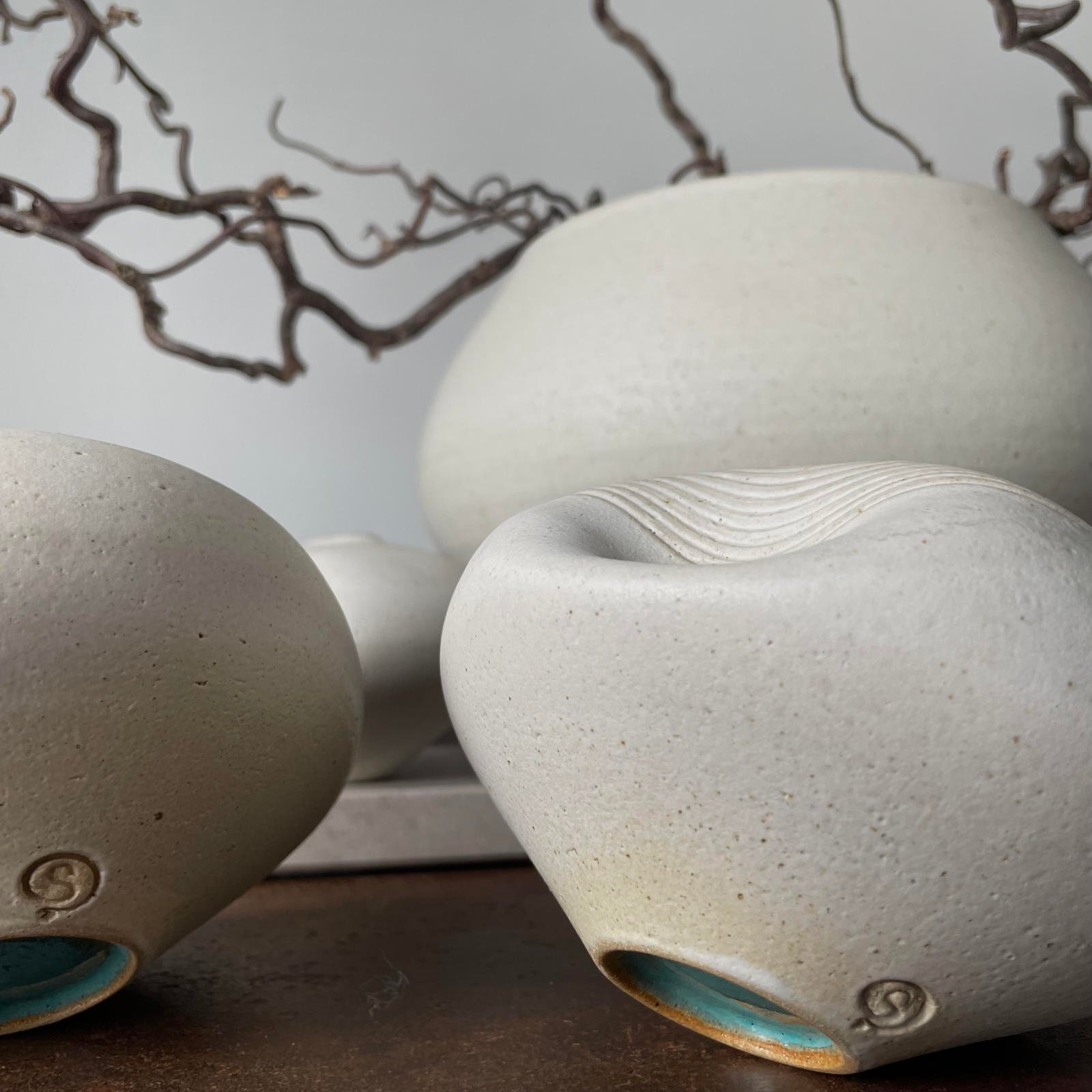
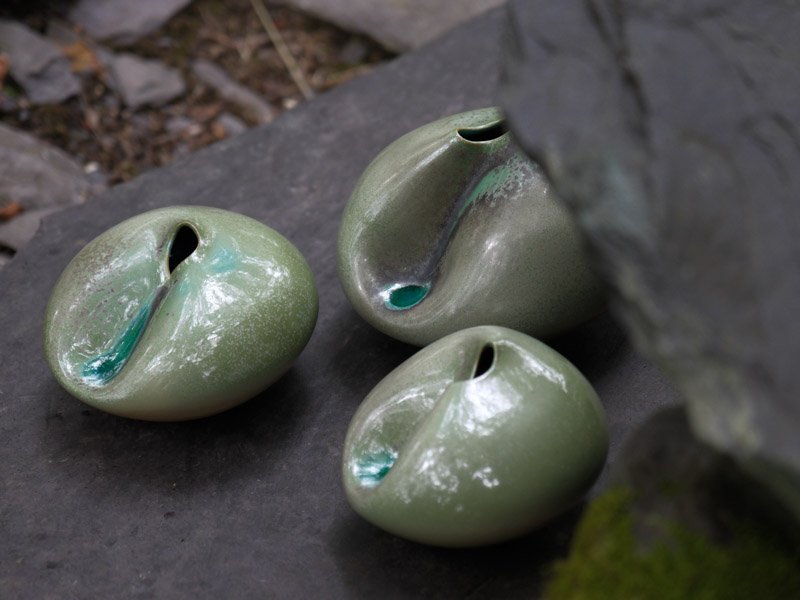
